One of the best company to work and IT solutions. Delivered product quickly and very fast. It was really mice working with them. I will give them move orders.
Common Mistakes Every Quality Management Team Can Avoid
Implementing a quality management system can be a tough and stressful task. What are the mistakes which quality control checklists and can avoid
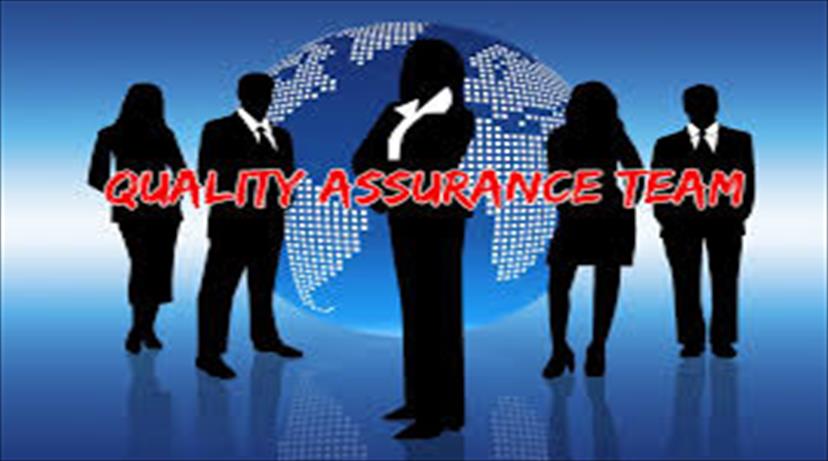
When it comes to project management, one aspect you cannot afford to jeopardize is quality. Regardless, multiple project executives are rendering quality errors without even understanding to make sure you do not jump into this type, we have put jointly a list of the quality management errors that you require to avoid in 2021.
One of the greatest errors that you can make when it comes to quality management is declining to take the crucial project management movements. It doesn't matter whether you are new to this sector or you have been supervising projects for years, project management classes can always assist. By taking a short read of this blog, you will remember the latest, trending, and greatly beneficial procedures for managing an operation, and a lot of this will concentrate on quality.
Your quality control staff is making errors again? Don’t get upset, just relax. It’s flawlessly typical for them to make errors. But, before they get you on the nerve regularly, perhaps you should predict it by specifying the difficulties. Yes, you can deter those mistakes of quality assurance from arising. It’s valid, still, that the quality control procedure should not arise in erroneous data because it influences customers’ satisfaction and security. In reality, even the extensively trained inspectors might make errors.
This blog will examine various popular mistakes that businesses frequently make. It might happen during the checking procedure itself as the mistake lies in tricky methods of quality assurance.
Only training some selected employees for QA Testing.
The company administration frequently speculates that people in organizational and supervisory roles completely comprehend their duties and thus are reliable. That is the explanation why most businesses prioritize training for front-line employees and underestimate training for the executives.
This is not true. The administrators equally require proper training to enforce the right quality control procedure. Their decisions will have an immense impact. When traditional employees make errors, it might cause business loss, but when the managers do that it might affect the company prestige.
Misunderstanding the products specifications and quality principles
Customers usually will hand the manufacturers a schedule of specifications of the software products and the quality control departments will cite to it during the inspection. The schedule might contain the size, dimension, color, ingredients, and other specs of a product. The list might also include the boundary of tolerance in products.
The inspectors might have spent a long duration testing the manufactured goods one by one. They might get bored and forfeit minor details or the requirement in the checklist. Accordingly, the products do not meet the criteria your customers set. Here is how you can crack it:
• Ensure that all units of the team comprehend the criteria of quality and products’ specifications through a briefing.
• Do inspection along with team rotation to make certain that the teams involved are capable and comprehensive enough for the training.
• Use compatible tools
There are tools that the inspection team utilizes to do quality control. Here are some errors that frequently happen:
• Forget to bring the tools for the checking procedure
• Bringing the incorrect tools
• Bringing the appropriate tools that are not appropriately calibrated.
Those problems arise in erroneous reporting. For instance, your manufactured products might not match the standard that was specified. During the inspection, if the team does not bring the correct tools to achieve the measurement, the outcome is not credible and the products’ deformity is not noticeable. To solve this, the inspection team should get a justification about the specification of the products and the tools that they’re going to utilize for quality control as comprehensively as possible.
• Management Representative (MR) involves in the reporting
Sometimes the MR team strives to satisfy the inspectors that certain deformities are okay, that the products can continue to operate. It might be problematic also if the management does not set the limitation for defect tolerance.
Thus, the inspection team requires to report all the defects that can not be resisted as per the criterion. The MR should collect the reports of the situation of the products and the specification checklists. So, the prosperity of the production is not founded on mere beliefs.
• Do the procedure manually
Quality control becomes very ineffective if the teams do it manually. Be it with sheet and pen or Excel document. This technique will consume your time portioning the products in piled documents. It deters you from assuring quality effectively.
Utilizing technology such as Manufacturing System enables you to function rapidly and extra accurately. After the production is finalized, you can instantly record the situation of the products founded on the criteria shortly. The cloud-based system enables everyone in charge to access the data from anywhere at any time.
In this blog, we present some characteristics of testing that are sometimes excluded -
1. Little time allotted for testing.
Testing is one of the project phases that are frequently cut out. This is difficult since the testing can offer you a category of positiveness that is unlikely to be kept in the project life cycle. The viewpoint that we are creating the product so nicely that we can test it in a brief period – is a phrase that should never be spoken of in your project meetings.
Testing should take a long duration because it’s crucial to do it correctly. Testing is not even something that you do once (unless you have good luck). You execute the test, locate mistakes, then rectify the mistakes, test again, then perhaps on your third test cycle you approve all the tests and can approve it off.
You should not schedule that you do a test once and be fulfilled with it: it’s a cyclical action until the tests pass. This moreover implies that you should have accessible testers for the entire time so that they can promptly respond when proliferation comes back to be tested again.
2. Scope of testing too limited.
Testing just the use cases is not sufficient. Anyone can go through the procedure and get an optimistic effect in a test: if the developers have created it to your specifications, it will possibly pass because you determine they’ve done a promising job.
You should strive for various testing strategies in your projects, and accordingly, you should enable the users to try “creative” ways to process data and get around the prescribed workflows, to understand whether your app is bug-free.
You can’t predict your end users (whether they are your colleagues in the company or members of the public) to comprehend how your product functions from the advent. They might be doing it badly because they don’t understand any better, so make sure that your testing wraps all characteristics and events, not just the normal ones.
3. Formal procedure not ascertained.
Each department or administrative area should sign off the testing – to assert that they are delighted it has been finalized sufficiently. This is crucial for your audit procedure and a bit of reserve covering for later on.
It doesn't matter the quality of your testing, someone at some point will inquire who has built the testing technique – and you should be careful in the proficiency that you’ve got the explanations. In other situations, you may look gullible.
4. Unskilled testers.
The businesses that have ascertained a lasting testing division that is utilized to test all aspects of advancements and products – are in a promising position. On the different side – multiple businesses hire testers with a specific background or aptitude – particularly when new systems are being executed and we do not have the proficiency in-house to test.
It is a nice pattern to contain the end-user representatives throughout the project, and hopefully, these people will have enough knowledge of the product to be able to test it completely. In different situations, it will possibly be the initial time the customers glimpses the outcome and they won’t understand how to utilize it, and of course – how to smash it for the objective that will get promising outcomes from the testing if your testers feel benefited and have the proficiency they require to test accordingly.
5. Terrible documentation.
It’s not sufficient just to execute your tests and determine that they are comprehensive. If you just click on the system exploring some strategies, that’s manipulation with the product, not testing it. The testing can not be severe unless there is something in composing that tells me what you have performed and what the effect was. As a minimum, you should document :
• Who executed the test;
• Date of tests;
• Environment testing carried out in (Development, Quality assurance, etc.)
• fundamental data points utilized in the testing;
• Test outcome (i.e., pass or fail).
If a test has failed, you should document what you found out it has failed: is that the aspect layout on the screen isn’t per the specification? This is the category of data that the team developers will require to make reasonable alterations and make the difficulty solved.
Another widespread mistake is taking the wrong turn by engaging stakeholders in quality control. The project team, comprising the stakeholders, needs to examine the project deliverables before they are adapted to assure that there are no mistakes and that quality criteria have been fulfilled. Plenty of project executives also make the blunder of neglecting to engage stakeholders in quality assurance, which is another large blunder.
Negligence to enhance project procedures will moreover lead to a drop in quality. You require to have a procedure development strategy in place to guarantee that the familiar difficulties related to procedures are prevented, including incompatible products, inadequate outputs, and taking too long. As with anything in a company, if you continue to be sluggish, you cannot anticipate keeping producing quality outcomes. You need to move ahead.
Another error to avert is not utilizing the right quality tools. Beneficial project managers require to have proficiency in the fundamental quality tools and understand how to utilize them effectively. This includes scatter charts, control charts, histograms, Pareto diagrams, check sheets, flowcharts, and cause-and-effect diagrams.
Plenty of project executives moreover fail to define requirements, and this is an expensive error. The development of requirements is a crucial portion of scope management. You require to analyze, document, and assess all of the subsequent requirements:
• Quality requirements
• Project requirements
• Transition requirements
• Solution requirements
• Stakeholder requirements
• Business requirements
Last but not least, the hugest error of them all is a failure to interpret quality. If you do not specify quality, how do you anticipate your project team to accomplish it? The quality says various things to several people, and you have to make sure that all project team members and stakeholders are on a similar page. Quality is the extent to which a project fulfills the requirements.
So there you have it – some of the extensively common errors that are made by project managers in 2021. If you avert the errors mentioned above in the blog, you can assure that the quality of your project is by company standards.
Conclusion
It’s very common for project inspectors to make mistakes one time or twice. That is why the company administration should have exact and thorough quality control techniques to deter recurring difficulties. If the documents, workers, and technical characteristics are following the strategies, the quality control will be extra beneficial and accurate.